For therapeutic goods to reach patients and consumers, they must be shown to meet Good Manufacturing Practices (GMP). GMP Certification is one such means of demonstrating this compliance. cGMP Certification, representing ‘current Good Manufacturing Practice Certification), is another term referred to by Regulatory Authorities in various jurisdictions, e.g. the US FDA.
In this blog we will help you understand the term ‘cGMP certification’ in the pharmaceutical industry, including:
There is a common misperception in the industry about GMP/cGMP Certification requirements. Industry newcomers often confuse ‘cGMP certification’ requirements with ‘Marketing Authorisation’ requirements. This article will help you understand the difference between these two industry terms, and why GMP training (GMP compliance training) is so important in the sector.
For GMP compliance training (certificate courses), click here.
What is GMP or cGMP?
The acronym ‘GMP’ stands for ‘Good Manufacturing Practice’. ‘cGMP stands’ for ‘current Good Manufacturing Practice’.
GMP Definition
GMP is the set of guidelines and principles enforced by the respective local regulatory authority (e.g., TGA, FDA, EMA, MHRA, etc.) which aim to ensure that the manufacture of therapeutic products* is controlled and consistent such that required quality standards at met. These principles cover all aspects of the manufacturing process – from the facilities and equipment used to the training of employees; even the testing of finished products.
*Whilst GMP also applies to food manufacture, this aspect is managed by different regulatory bodies to pharmaceutical products and medical devices (e.g. FSANZ vs TGA in Australia) and is outside the scope of the blog.
Resources: Learn GMP requirements and the “10 Golden Rules of GMP” via online GMP training courses.
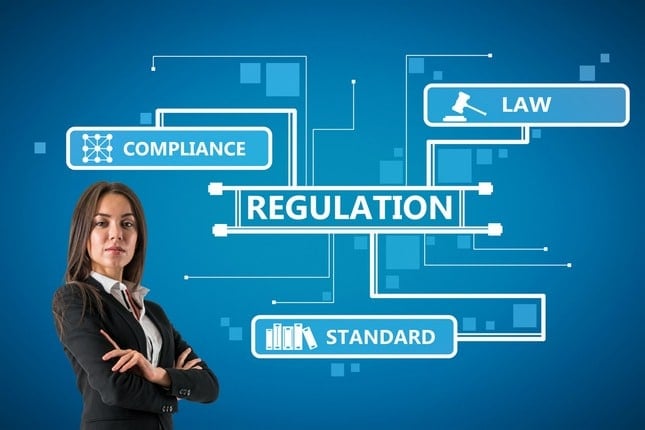
GMP & cGMP Compliance Audits
“Affirming personnel adhere to GMP rules helps protect public health and safety. GMP compliance audits and self-inspections help ensure that a therapeutic product (e.g., pharmaceutical products, medical devices, software as a medical device) is suitable for its intended use, and is safe and effective. GMP compliance also helps ensure product traceability in the event a product recall is required.”
How do you demonstrate your compliance with GMP?
There are a number of ways that business owners can demonstrate the compliance of their therapeutic products to Good Manufacturing Practice (GMP), the need for which – from the perspective of cGMP certification – will be dependent on the location of the manufacturer, sponsor and distributor.
Manufacture Licence
IF:
then you need a manufacture licence** under the Therapeutic Goods Act 1989.
GMP Clearance
IF:
you need GMP clearance. Read on.
*The TGA manufacturing licence and GMP certification processes are not applicable to medical devices. For more information, see Manufacturing medical devices: where to start.
**Manufacturing licensing is outside of the scope of this blog about cGMP certification. Further information about the requirements and steps for manufacturing licences is available in Australian manufacturing licences and overseas GMP certification
GMP Clearance
GMP Clearance is a non-statutory mechanism used to verify that overseas manufacturing sites comply with the principles of GMP for the products being supplied to Australia.
The TGA may issue GMP clearance to sponsors of a medicine or API that is manufactured overseas if there is acceptable evidence demonstrating that the overseas manufacturer complies with the principles of GMP.
Sponsors are required to obtain GMP clearance for overseas manufacturers of their registered or listed products to satisfy the Therapeutic Goods Act 1989, and ensure the safety, quality, efficacy and timely supply of therapeutic goods for Australian consumers.
GMP clearance can be obtained by an Australian sponsor* who:
- can use the MRA or CV pathways to GMP clearance instead of requesting TGA certification
- can obtain GMP certification from the TGA if the MRA and CV pathways are not appropriate
*A sponsor is a person or company who does one or more of the following:
- exports therapeutic goods from Australia
- imports therapeutic goods into Australia
- manufactures therapeutic goods for supply in Australia or elsewhere
arranges for another party to import, export or manufacture therapeutic goods.
MRA or CV pathways to GMP clearance
GMP clearance can be obtained per manufacturing site by:
- a Mutual Recognition Agreement (MRA) desktop assessment if the manufacturer you are seeking GMP clearance for is located within the borders of a MRA country, and has been physically inspected by that country’s regulatory authority.
- a Compliance Verification (CV) desktop assessment if the manufacturer you are seeking GMP clearance for does not meet the criteria for the MRA pathway and has been physically inspected by a regulatory authority that has an agreement or arrangement with the TGA.
Further information about these pathways is available in GMP clearance guidance.
GMP Certification
GMP certification is how we determine that certain therapeutic goods manufactured overseas and intended for import and supply to Australia comply with GMP requirements.”
“Only Australian manufacturing sites can obtain a manufacturing licence.
Overseas manufacturers can instead obtain GMP certification following a successful on-site inspection by the TGA.
GMP certification applications are required to be submitted by the Australian sponsor or an agent acting on the Australian sponsor’s behalf.
GMP certification is usually only requested if it is not possible to obtain GMP clearance via the Mutual Recognition Agreement (MRA) or Compliance Verification (CV) pathways, for example, due to lack of evidence.”
How to achieve GMP certification (Australia example)
The process for achieving GMP certification is fully and clearly recorded in Australian manufacturing licences and overseas GMP certification; A step-by-step guide for Australian manufacturers of therapeutic goods. (1 December 2021)
This document details the more than twenty steps required, from understanding whether you need GMP licensing or clearance, through inspections, to the granting/issuing of licences/certifications.
This document details:
Other requirements
Being able to prove that your imported product is GMP-compliant is not the only permission you need to seek before your product can be supplied to the market.
Products that are distributed on the Australian market must also have a valid market authorisation and, in most cases, entry on the Australian Register of Therapeutic Goods (ARTG).
Overview of applying for a Market Authorisation details the process for seeking this approval.
Also: If you’re new to therapeutic goods regulations, the TGA provides a very helpful resource including a good basic review of the scope of the TGA’s operations, supply pathways, sponsor responsibilities, goods classification and regulations, and licensing/certification. You can find it here: Regulation essentials.
Need to learn more? Explore GMP Training options and important regulatory compliance topics and standards.
Authors: Eleanor Redding and Carla Medlin (Editor: CM)
cGMP Certification Resources and references
EU GMP: cGMP Certification in the Europe Union (EU)
Excerpt: “Good manufacturing practice (GMP) describes the minimum standard that a medicines manufacturer must meet in their production processes. The European Medicines Agency (EMA) coordinates inspections to verify compliance with these standards and plays a key role in harmonising GMP activities at European Union (EU) level.”
Click here for further information
UK GMP: GMP Certification in the UK
GMP compliance for UK companies and medicinal products is overseen by the Medicines and Healthcare products Regulatory Agency (MHRA).
Excerpt from the MHRA (GMP Certification):
Good Manufacturing Practice (GMP) certificates: A certificate of Good Manufacturing Practice (GMP) is issued to a manufacturer if the outcome of the inspection confirms that the manufacturer complies with the principles of Good Manufacturing Practice.
FDA GMP requirements
FDA GMP compliance requirements are discussed in the US FDA’s CFRs*.
CFRs = Code of Federal Regulations.
Refer to the following CFRs as appropriate to your pharmaceutical product and/or medical device:
- 21 CFR Part 314 For FDA approval to market a new drug.
- 21 CFR Part 210. Current Good Manufacturing Practice in Manufacturing Processing, packing, or Holding of Drugs.
- 21 CFR Part 211. Current Good Manufacturing Practice for Finished Pharmaceuticals.
- 21 CFR Part 212. Current Good Manufacturing Practice for Positron Emission Tomography Drugs.
- 21 CFR Part 600. Biological Products: General.
Click here for FDA GMP information.
GMP Training for FDA CFRs 820 (Medical Devices)
GMP Training for FDA CFRs 210 & 211 (Pharmaceutical Products)
Note: Responsibilities for GMP start at the stage of sourcing and receiving raw materials and intermediates for further production, packaging, labelling, and distribution. GMP responsibilities continue through the storage (warehousing) and distribution of pharmaceutical products/therapeutic goods, e.g. distribution to patients or consumers.
Examples of warehouse/storage requirements (GWP) and distribution (GDP) rules can be found in the following two training courses for GMP compliance:
Good Warehouse Practice (GWP) training
Good Distribution Practice (GDP) training
For additional certificate GMP training courses, click here.
Option: PharmOut Pty Ltd offers intensive 1-day GMP training workshops led by industry experts. Click here to learn more about facilitated GMP presentations, public workshops, and onsite GMP training options.
Last updated on July 6th, 2023 at 09:31 am